Downhole Logging Tools
Selecting Logging Tools
The selection of specific downhole logging tools for a particular expedition is an ongoing procedure that starts with the proponents and (usually) ends when the Program Plan is approved. The standard tool strings that measure the basic formation properties are always on the ship, often accompanied by one or more of the specialty tools. Specialty tool use is dictated by the scientific objectives of the expedition, and by the size of the year's budget for specialty tools. The operational plan for logging is determined at the pre-cruise meeting, usually held 6 to 8 months before the cruise, and is included in the expedition prospectus. Confirmation of the logging plan and time estimates are made onboard before each site at the "pre-site" meetings.
The table below displays the various logging measurements associated with specific scientific or technical applications. Click here to view a list of the tools available for each measurement.
Most of the basic petrophysical and lithological logs (density, porosity, resistivity, velocity) are acquired with the Triple Combo tool string, which is always run first. This string also measures the borehole width, an important indicator of borehole and log quality. The FMS/Sonic is usually run next: the FMS resistivity image reveals the fine details of the formation, and the sonic velocity completes the basic logs. The specialty tools are run, usually in order of scientific importance. Seismic tools are usually run last, because due to the fact that they are clamped against the borehole wall they can destabilize the hole, and their light weight and large caliper arm makes them prone to getting stuck.
When time is short, or when there are adverse logging conditions, the Logging Staff Scientist has the responsibility of preserving the integrity of the logging plan and making appropriate changes to it if necessary. He will keep in regular contact with the Operations Superintendent and the Co-Chief Scientists, so as to be up to date with the latest operational developments. Shipboard scientists should understand that it is the Logging Staff Scientists job to act as an advocate for the logs, based on their scientific merit - not just because they are part of the logging plan in the scientific prospectus.
The principles to keep in mind when prioritizing tool strings are:
- To get the logs most relevant to the leg's scientific objectives.
- To run the tool strings most likely to get good results.
- To minimize the risk of harming the tools or getting them stuck down the hole.
The scientific, environmental, and technical issues relevant to tool string selection are described briefly below.
Scientific Issues
Lithology
The natural gamma and photoelectric factor (PEF) logs yield information on aspects of the chemical and mineralogical composition of the formation, which can be used to infer lithology (see individual tool summaries). This information can then be used to complement the core record, to fill coring gaps, to pinpoint boundaries, etc. The absence of gaps in the logs makes them particularly useful for studies of sediment cyclicity, where a complete record is essential.
Petrophysics
The porosity, density, resistivity, and sonic velocity logs collect petrophysical and geotechnical information about the penetrated formations. In sediments, the general trend in these logs is dominated by increasing consolidation with depth. Deviations from this trend are caused by lithological change, lithification (cementation), under-consolidation (due, for example, to high pore fluid pressure), or the presence of gas hydrates (hydrate in the pore space increases resistivity and sonic velocity). The principal advantage of these logs over the equivalent core measurements is that the logs record the in-situ property, whereas the cores are expanded and depressurized, and can suffer from end-effects and biscuiting.
Relation to the seismic section, synthetic seismograms
The borehole seismic tool (VSI) is used for checkshot surveys (to obtain a depth-traveltime relation) and zero-offset VSP experiments (to obtain seismograms at the site). The depth-traveltime relation can also be derived from the sonic velocity log, which together with the density log and seismic source wavelet combine to make a synthetic seismogram. Thus, reflectors on the seismic section can be correlated with lithological or petrophysical changes in the borehole.
For almost every expedition there is an extensive interpreted set of site survey seismic sections, and so it is of great importance to associate borehole information with mapped seismic reflectors.
Structure and fabric
FMS, UBI, LWD-geoVISION, LWD-adnVISION, and LWD-EcoScope data provide physical property images of the borehole wall, showing detailed structural (faults, fractures), sedimentological (turbidites, beds, bioturbation, concretions, clasts), and igneous (veins, alteration, and basalt pillows, breccias, and flows) features.
Crustal stress and anisotropy
If horizontal stresses in the formation are not uniform, borehole enlargements, or breakouts, form marking the minimum horizontal stress direction. The UBI, LWD-adnVISION, and LWD-EcoScope data measure the shape of the borehole and directly image breakouts. The full-coverage resistivity images obtained by the LWD-geoVISION also show breakouts as vertical bands of low resistivity. Finally, the caliper arms of the FMS tool tend to follow the major and minor axes of the borehole if it is elliptical, and thus can also be used to infer stress orientation.
The Dipole Sonic Imager (DSI) can reveal shear wave anisotropy, which may be due to crustal stress or a preferential rock fabric.
Heat and fluid flow
The MTT tool records the temperature of the borehole fluid, which typically increases downhole. The borehole fluid temperature equilibrates towards the actual formation temperature over the course of the logging run, and thus gives a lower limit to the actual formation temperature. Where formation fluids locally enter the borehole, they will cause an anomaly in the temperature log.
Environmental Issues
The state of the hole for wireline logging can be assessed from the conditions experienced during coring. Before logging, the Logging Staff Scientist will confer with the Operations Superintendent and drillers about the general condition of the hole, and whether there are any "tight spots" or likely washouts. The Schlumberger Engineer, the Operations Superintendent, the Drilling Superintendent, the drillers, and the core technicians all have a wealth of experience in dealing with adverse hole conditions, and should be able to advise on specific matters such as how long to spend trying to break through bridges, what the risk to tools might be, how to retrieve stuck tools, and so on.
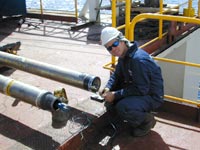
Logging-while-drilling (LWD) tools may be assigned to expeditions where hole conditions are anticipated to be unsuitable for conventional wireline logging. Currently available LWD tools include the geoVISION, adnVISION, EcoScope, proVISION, sonicVISION, and Resistivity-while-coring tools. Measurement-while-drilling (MWD-TeleScope) tools are used when real time acquisition of downhole data is required, for example, to monitor borehole fluid pressure for safety.
Time-limited logging
Although adequate time for logging is usually allocated in the expedition prospectus, it is not uncommon for unforeseen events (bad weather, difficult formations slowing the pace of coring, etc.) to reduce the actual time available for the logging program at a given hole. In this case, the Logging Staff Scientist will discuss with the Co-Chiefs the relative merits of allocating extra time to carry out the original program, cutting back on repeat runs or even forgoing a tool string entirely. The Triple Combo will still be run first, but the others should be prioritized according to the leg objectives.
Bridged holes
Some holes may contain constrictions (bridges) that hinder the tool strings descent into the hole. The heavier tool strings (triple combo and FMS/Sonic) have a better chance of passing through a bridge than the lighter tool strings (VSI); therefore, these are run first. One cause of bridges is swelling clays; this phenomenon can be combated by adding KCl to the drilling mud, although this will degrade the natural gamma potassium log.
Blocked holes
In wireline logging operations, the bottom-hole assembly (BHA) is generally lowered 70-100 mbsf and logging measurements are taken in the open hole between the BHA and the base of the hole. There are various options if the tool string cannot penetrate beyond a certain depth in the hole. If the blockage is near the base of the hole, it is probably best to just log the open interval above the blockage. If the blockage is midway down the hole, several options exist: 1) log only above the blockage; 2) dismantle the logging cable and lower the BHA to ream the blockage, then raise the BHA back to the original position; or 3) lower the BHA below the blockage and only log below it. If the blockage is near the top of the hole, it is likely that there will be similar blockages further down and the hole is unloggable, but dismantling the wireline cable and re-reaming the hole is always an option.
Wide holes
Wide holes can result in poor contact between the tool sensor and the borehole wall, and hence degraded logs. Affected tools are the HLDS and APS (max caliper extension 18 in), the FMS (max 16 in), and the VSI (max ~18 in). The borehole diameter is measured by caliper during the first (triple combo) run.
High heave conditions
The wireline heave compensator (WHC) reduces the effect of ship heave on tool motion, but higher heave conditions lead to increased uncertainty in the downhole tool depth, particularly if the heave is too great (more than 3 m) for the WHC to be used. Increased tool motion (up-down oscillation) poses a risk to those tools with caliper arms (e.g., the HLDS and FMS), as there may be downward tool movement even when logging upwards; higher logging speeds will help. Additionally, high heave makes the process of bringing the tools back into the pipe from the open hole after logging more difficult because of increased differential motion between the pipe and the tool string.
There is an increased risk of the wireline cable slipping on the cable reel when lowering the tools down though the pipe, especially at the start of the descent, because initially there is only a small weight to provide tension in the cable. Tools must be lowered slowly, adding to the logging time particularly in deep waters. The risk of cable slip is worse with the lighter tool strings (for example, VSI).
High temperature conditions
When in a high temperature environment (such as a hydrothermal ridge system), careful attention is paid to the temperature measured by the cablehead or wireline tools (for example, the MTT). It is important not to exceed the tool temperature ratings. Circulating water in the hole immediately prior to logging will cool the hole for a period of time. Some measurements, such as resistivity, are temperature dependent.
Technical Issues
Logging tool limitations
Wireline logging operation is limited to downhole tools with a diameter of 3.75 in or less. All tools listed in the tool section of this document can be deployed in a standard bottom hole assembly (BHA). The absolute maximum tool diameter which can be run in a standard BHA is 3.81 in, but this is pushing the tolerances to unsafe limits
Stuck/lost tools
This issue is discussed in more detail on the stuck/lost tools page. Needless to say, every effort should be made to avoid getting any of the tools stuck in the hole. The loggers are required to fish for any tool that is stuck or lost. It is particularly undesirable to lose tools that contain radioactive sources (such as the HLDS) or neutron generators (APS). Losing one of these tools would require cementing of the hole, a time-consuming process.
Dedicated logging holes
The more time spent coring a hole, the wider and more unstable it will become. For this reason, a fresh hole is occasionally drilled to obtain better logs. On the other hand, the additional time ire qui red is usually prohibitive, and it is useful to have cores and logs from the same hole to aid comparison.
Logging APC/XCB vs. RCB holes
The logging tools can pass through the APC/XCB bit, whereas the RCB bit has to be "dropped" at the bottom of the hole before logging tools can pass through. The hole cannot be deepened or bridges reamed after the RCB bit has been dropped. The RCB bit is about 2 in narrower than the APC/XCB bit, so the RCB hole is less likely to be wide, and consequently better for the FMS.
The lockable flapper valve (LFV) and go-devil
The lockable flapper valve (LFV) is included in the APC/XCB bottom-hole-assembly to avoid backflow into the drill string. The go-devil is a solid aluminum cylinder that opens the LFV. Details on the deployment and operation of the go-devil are given in the go-devil link in the Other Equipment section on the tool strings and tools page.
Third Party Tool Support
USIO/LDEO provides support for broad aspects of third-party wireline downhole tool deployment. Third party tools are designed and developed by investigators at institutions involved with IODP and are reviewed by the relevant program advisory panels for deployment on the JOIDES Resolution. USIO/LDEO Logging Services provides support to third party investigators in the areas of data acquisition systems and software, tool design and manufacturing assistance, and tool testing.
The need for custom-designed surface instrumentation and acquisition systems has been addressed through the development of a multipurpose data acquisition system installed in the telemetry lab. This system offers numerous benefits, including a standard computer platform from which to launch acquisition software and a work space in the acquisition area devoted to third party equipment. Data telemetry software currently available includes modules utilizing a Windows XP/LabView graphic environment for acquisition of the following data types:
- Temperature and pressure
- Depth and heave
- Acceleration
Third-party tool support also includes the design and production of a cablehead crossover that allows third party tools to connect to the Schlumberger cablehead via an inexpensive, modified off-the-shelf connector. In addition, a downhole Multi-Function Telemetry Module (MFTM) is also available for real-time downhole data transmission to the telemetry lab. Hardware components currently available for third party tool support at LDEO include:
- PC-based data acquisition system at LDEO and on the JOIDES Resolution
- Crossover for connecting third party tools to a Schlumberger-style cablehead
- Telemetry connection to a depth measurement system
- Access to pressure test vessel capable of 10,000 psi
- Access to 740 foot test hole at LDEO
- 22,000 feet of 7-46PXS wireline with terminations
Assistance during the development of third party tools is provided through USIO/LDEO personnel and the facilities available at LDEO. On-site facilities are available to assist in manufacturing, assembly, and pressure and field testing. Interested investigators should contact USIO/LDEO Manager of Engineering and Technical Services Gerardo Iturrino at iturrino@ldeo.columbia.edu.